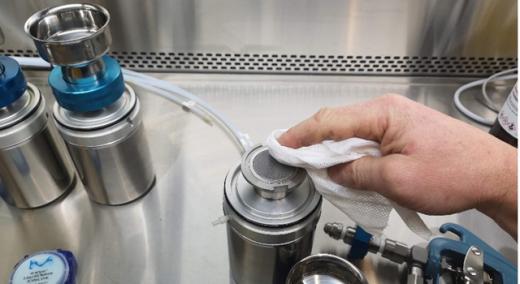
This article will focus on a sampling method that is commonly used to analyze fluid: direct liquid filtration. Simply put, direct liquid filtration is a sampling technique used to determine the particles present in a liquid.
ADVERTISEMENT |
In direct liquid filtration, the liquid with suspended particles is filtered through a membrane filter so the particles collect on its surface. Then the filter membrane is imaged with a light microscope for particle analysis. Keep reading to learn more about this fluid sampling method, including best practices to follow when extracting a fluid sample for cleanliness analysis.
Small particles, great effects: The importance of clean fluids in machinery
Shipping, energy, offshore, and pharmaceuticals are some of the industries that have discovered the benefits of clean fluids.
Milling machine using oil
…
Add new comment