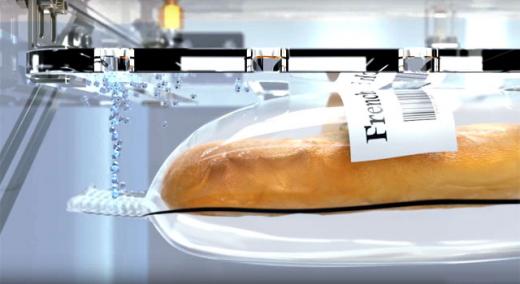
Many industrial products must be leak-tight. For example, food, cosmetics, or pharmaceutical packaging, but also products such as lights in the automotive industry, electronics, or plastic components. But how can manufacturers test the leak-tightness of their products?
ADVERTISEMENT |
The entry-level solution is to test in a water bath. This is a simple yet effective method. The test specimen is held under water, and the tester watches for rising air bubbles. Very intuitive. In principle, it’s much like patching a bicycle tube, except that the product is not inflated but tested in a vacuum chamber. The product inflates itself, and bubbles escape from leaks. The important thing is that you not only know that the packaging is leaking, but you also immediately recognize where. This allows weak points in the process to be detected and eliminated. The LEAK-MASTER EASY makes this process economical and uncomplicated.
…
Add new comment