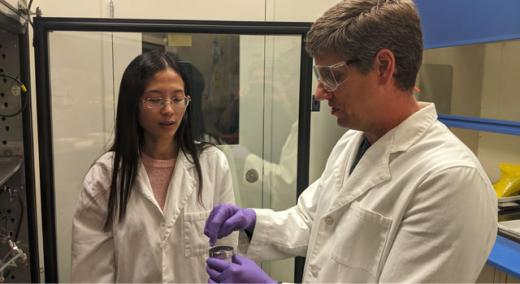
On August 29, 2005, I was starting my first semester teaching freshman environmental engineering majors at Humboldt State University in Arcata, California. At the exact same time, Hurricane Katrina hit Louisiana and Mississippi with 190 kph (120 mph) winds and a storm surge in excess of 6 meters (20 feet). Levees failed, flooding more than 80 percent of New Orleans and many surrounding areas. This tragedy left more than 1,800 people dead, many of whom had been trapped in their own homes. It took nearly six weeks for the water to recede, exposing more than 130,000 destroyed housing units.
…
Comments
Formaldehyde in Wood Products
Glad to hear you are working on this. In the 70's, while working for Georgia-Pacific, I became aware of a health issue in Russian school children caused by formaldehyde release from wooden school furniture. We discovered this by technical literature searches which were at that time in their infancy. Our search system used a program developed by the Systems Development Corporation and included outside literature as well as company technical reports which we keyword coded and sent to SDC. As far as we know, this was the first private computer searchable database in the USA. Deanna Morrow and I published a paper on our work in TAPPI in 1972.
As a producer of formaldehyde and its use in many products our company was alerted to potential problems. I recall making a trip to the US Forest Products Laboratory in Madison WI to discuss the issue. They had developed a test method using as I recall purpald to detect formaldehyde release and something of its concentration.
I know there has been much work since that time. Thanks for the update.
William H. Pound, PhD, retired
Add new comment