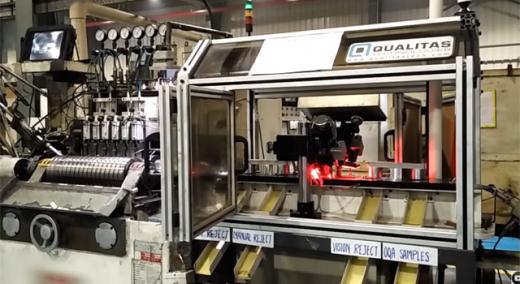
Bearings are important components of mechanical equipment. They are specifically designed to convert the direct friction from parts in relative rotation into rolling friction or sliding friction of the bearing. As a result, bearings are extremely important in reducing the friction coefficient and ensuring the long-term stable operation of a machine.
ADVERTISEMENT |
The bearing surface and bearing rollers both have an important impact on the installation performance, use, quality, and life of the bearing. Common defects on a bearing roller’s surface, such as wear, cracks, bruises, pitting, scratches, or deformation, can lead to machine vibration and noise, accelerate oxidation and wear, and even damage the machine. It is thus paramount to inspect the surface of the bearing as well as the bearing rollers to prevent defective products from entering the market.
…
Add new comment