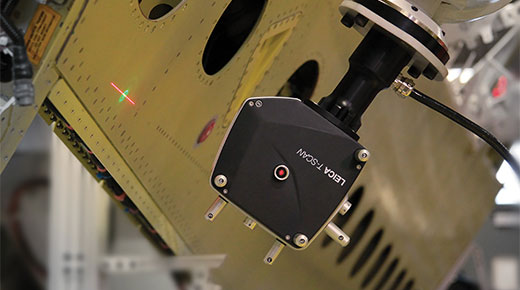
Sponsored Content
Wichita, Kansas, is known as the “Air Capital of the World.” This is due in part to the National Institute for Aviation Research (NIAR) at Wichita State University, an advanced aircraft manufacturing laboratory. The area is home to notable aerospace and defense OEMs, including Boeing, Hawker Beechcraft, Bombardier Learjet, Cessna, Spirit Aerosystems, and Airbus Americas.
ADVERTISEMENT |
In the competitive world of advanced aircraft manufacturing, developing world-class talent that can drive innovation is essential to the longevity of the industry. This is where NIAR is uniquely positioned to assist both the local and global need for highly-skilled aircraft assembly professionals.
…
Add new comment