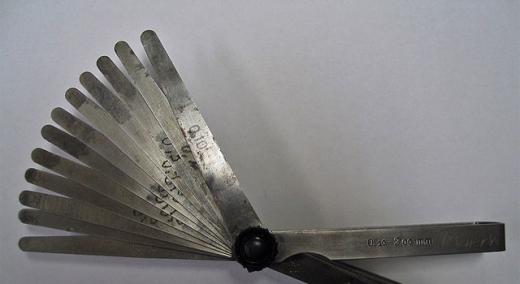
Body
Attribute gauges are a type of measurement instrument or process that gives a binary pass/fail measurement result. Examples of attribute gauges include go/no-go plug gauges, feeler gauges, and many other types of special-purpose hard gauges. Many visual-inspection processes may also be considered attribute gauges. They are commonly used in manufacturing for product verification. Knowing the accuracy and capability of these measurements is therefore vital for a comprehensive understanding of quality in manufactured goods.
…
Want to continue?
Log in or create a FREE account.
By logging in you agree to receive communication from Quality Digest.
Privacy Policy.
Add new comment