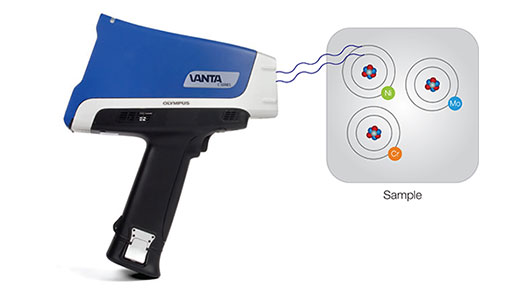
Sponsored Content
High-volume manufacturers need fast, nondestructive testing methods to help avoid material mix-ups and to meet customer quality requirements. Quality assurance (QA) inspectors are responsible for evaluating incoming raw materials by determining their elemental makeup and assessing the structural integrity of products on the production line. QA inspectors need a reliable solution that helps them get both jobs done, quickly and efficiently.
ADVERTISEMENT |
Well-built products begin with proper materials
Positive material identification of incoming materials is especially crucial to the overall quality of welded materials, as using the wrong material can lead to structural weakness and product failure. Inspectors seeking fast, accurate, alloy verification frequently turn to handheld instruments, such as the Vanta X-ray fluorescence (XRF) analyzer.
…
Add new comment