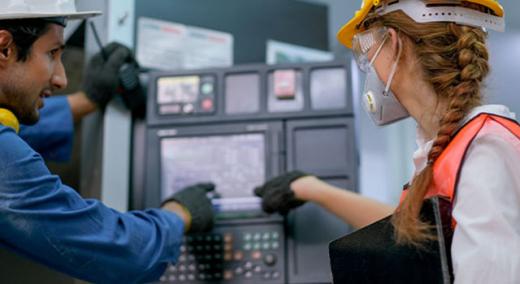
Even with advancements in technology and automation, the frontline workforce remains essential to modern manufacturing operations. In fact, 72 percent of factory work is still performed by people.
ADVERTISEMENT |
This means that operators, technicians, and line managers are all your biggest operational risks.
Manufacturing organizations have the same goals—reduce waste, improve quality, and increase efficiency. But operational excellence is an evolving target.
With the generational shift happening in the frontline workforce, manufacturing employees are facing a new set of challenges that directly affect these goals in unique ways. It’s time to understand the needs of the frontline workforce and how new strategies can empower them to perform their best.
…
Add new comment