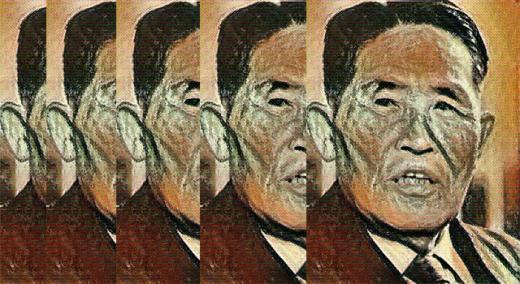
Shigeo Shingo is one of my heroes in industrial engineering. He had a great mind that thrived on curiosity. Today I am looking at Shingo’s Whys. This is in contrast to Taiichi Ohno’s 5 Whys method.
ADVERTISEMENT |
Ohno’s 5 Whys method is one of the tools in Toyota Production System to get to the root cause of an issue. When you see a problem, you ask, “Why did that problem happen?” When you get an answer to that question, you then ask, “Why did that problem No. 2 happen?” and so on until you get to the root cause. When you eliminate the root cause, the problem is solved.
This approach assumes a direct and linear cause-and-effect relationship. And depending on the user’s expertise and experience, you can get different results. A tool like 5 Whys is user-dependent and one-dimensional. It is appropriate for necessary causes; it may not be appropriate for sufficient causes. Its usefulness certainly diminishes as complexity increases.
Shingo’s Whys are not in relation to Ohno’s 5 Whys, but another set of questions, known as 5W1H. They are:
1. Who?
2. What?
3. Where?
4. When?
5. Why?
6. How?
…
Comments
Critical Thinking
Excellent article! Thanks for breaking down the 'boxes' that now-'conventional' wisdom is contained in, and constrained by -- for seeing that such 'wisdom', although useful and powerful, is still at root, just an idea ..... and that ideas can still be extended, and even more useful and powerful ideas can be creatively thought, and applied. "There are many means", to be creatively discovered, and discovered, and discovered.
MODAPTS Tracks Employee Motion in Detail
Manufacturers around the globe use MODAPTS to analyze and optimize employee motion during production, just as Shingo suggested.
In service industries, value stream mapping and spaghetti diagramming eliminate unnecessary delays and motion which consume up to 57 minutes of every hour. I call this the 3-57 rule. Employees are only working on the product or service 3 minutes out of every hour.
It's possible to cut cycle time by 50% or more in most unanalyzed processes. Few companies embrace speed as the "healing app."
Add new comment