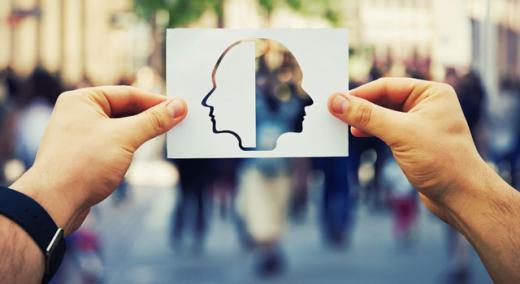
I just received and read the “2021 ASQE Insights on Excellence Executive Brief.” The brief examines how quality initiatives are progressing in the digital era, based on the views and experiences of 542 executives and quality professionals from global enterprises. Here we go again, I thought.
ADVERTISEMENT |
Yes, technology drives change, change drives new quality issues, and new quality issues drive quality professionals to come up with new quality performance metrics and enhancements. I’ve read these same platitudes for years. We believe that systemic issues of quality can be solved with new programs, new spreadsheets, or new ways to calculate quality performance. Obviously, some of the solutions hit the root cause of a specific issue. But the systemic factor, which has always been present and is at the heart of all matters of quality as technology drives change, is management.
Management in most companies is the root cause of not keeping up with technology or the market, or the generational changes needed as younger employees are hired. It’s all about culture and behaviors. As an example, let’s compare and contrast safety and quality.
…
Add new comment