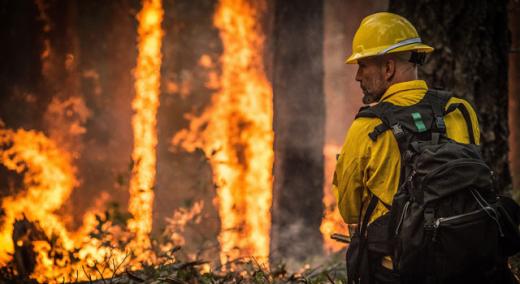
Body
Perhaps the worst quality failure of modern times is Boeing’s 737 Max disaster.
…
Want to continue?
Log in or create a FREE account.
By logging in you agree to receive communication from Quality Digest.
Privacy Policy.
Comments
Just a thought
Can Nokia company be considered as a victim of "normalcy"? --- And your article is really good and a worthwhile read.
Add new comment