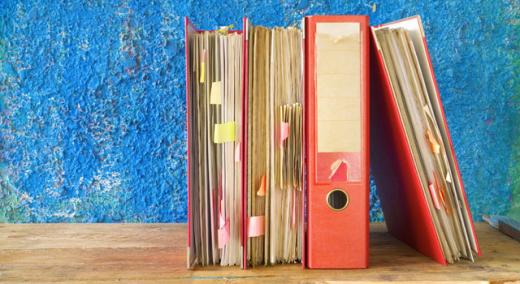
Every company uses a system to understand the requirements and inputs of its customers, and then plans to deliver outputs meeting those requirements as a conforming product or service. The International Organization for Standardization (ISO) publishes management system standards that, when correctly interpreted, enable companies to systematically and consistently provide desired outputs while addressing risks.
ADVERTISEMENT |
Using the framework provided by ISO, companies can design systems and processes that work together to deliver desired outputs (i.e., products or services). An organization should endeavor to define its outputs accurately, after understanding customer requirements, both stated and unstated. ISO standards allow companies of any size and industry to implement them; hence, a lot is left open to interpretation.
Despite this, certification to these management system standards delivers confidence to potential and existing customers that the company is implementing a process with the intent of continual improvement. Across the globe, an ISO management system certification, such as ISO 9001, gives confidence of a certain basic framework being implemented and followed.
…
Comments
Documentation Must Resemble ISO
The point is well taken that a QMS should be tailored to the culture and processes of each organization. The downside to using a different numbering system or structure to the documentation is that you will have to build a crosswalk for your external auditor.
They are in 2-3 companies a week and their brain is hard-wired to the Standard and its numbering system. Using a different structure will increase audit hours and lead to confusion by the auditor. If it is a new registration, the quality manual might not pass the desk audit by the registrar.
RE; RE Documentation must resemble ISO
Indeed a QMS should be tailored to the culture and processes of each organization. In my view, this is far more important than squeezing audit hours or satisfying hard-wired auditors. New technology can help us serve both sides as IT_enabled DMS systems facilitate easy cross-referencing of procedures/processes and ISO requirements. This will support a QMS tailored for the organization and keep costs in control, even with hard-wired auditors.
Management System aligned to the Standard
I agree. Apart from the IT and availability of tools, the basic principle is to write a management system (MS) for the organization. Not for the auditors.
Management System aligned to the Standard
Dear Tom,
With due respect to your views and concerns here are my thoughts. First please don't write a management system (MS) for auditors. Audits are meant to provide inputs for TM to better resource the systema and appreciate risks. The system should be written for the users of the system. The Employees of the organization work to their procedures to meet requirements and produce confirming products and services. The MS therefore (per clause 4.4 of ISO 9001) should be designed to processes and provide the interactions between processes. A system written to clauses will never meet this requirement nor be user friendly. The very purpose of the MS is lost. For certification or otherwise, it is the auditors job to audit and see confirmity. Lot of the auditors are confused because they come in search of non-confirmty. Good auditors should be auditing to look for conformity. It is a total waste of money if the system is written for the purpose of auditing!
IJ
Add new comment