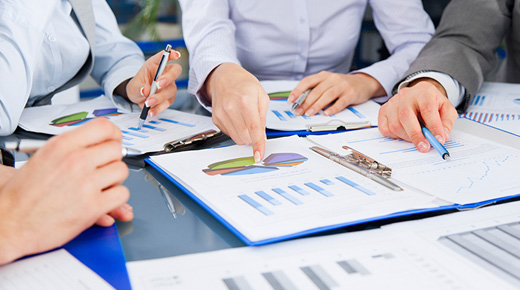
Roughly 7 in 10 manufacturers have implemented lean manufacturing principles in their organizations, with 5S, Six Sigma, and kaizen representing the most popular strategies today.
ADVERTISEMENT |
One tool that supports these specific approaches and lean manufacturing principles more generally is a layered process audit (LPA) program. LPAs draw auditors from all management layers and departments to verify mission-critical processes on a daily basis.
Let’s examine how LPAs align with lean manufacturing principles, providing a structured approach to unlock the biggest benefits of this popular quality methodology.
…
Add new comment