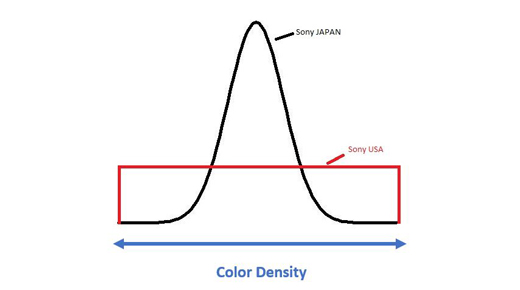
I am a quality manager by profession. Thus, I think about quality a lot. How would one define “quality?” A simple view of quality is “conformance to requirements.” This simplistic view of quality lacks the complexity that it should have. It assumes that everything is static, the customer will always have the same requirements, and will be happy if the specifications/requirements are met.
ADVERTISEMENT |
However, customer satisfaction is a complex thing. Customers are external to the plant that manufactures the widget. Thus, the plant will always lack the variety that the external world will impose on it. For example, let’s look at a simple thing like a cell phone. Theoretically, the purpose of a cell phone used to be to allow the end user to make a phone call. Think of all the variety of requirements that the end user has for a cell phone these days—internet, camera, ability to play games, ability to use productivity apps, stopwatch, alarms, affordability. Additionally, the competition is always coming out with a newer, faster, and maybe cheaper cell phone. To paraphrase the Red Queen from Alice in Wonderland—the manufacturer has to do a lot of running to stay in the same place—to maintain the share of market.
…
Comments
Kano Categories
Thanks for the great article Harish - I like the very concise explenation of the Kano model.
One question: what's your opinion regarding the reverse and questionable category of the model? I know that there are some people who don't consider those two categories at all. I believe they are not part of the original model but were added later? Just wondering what your thoughts on this are :)
Add new comment