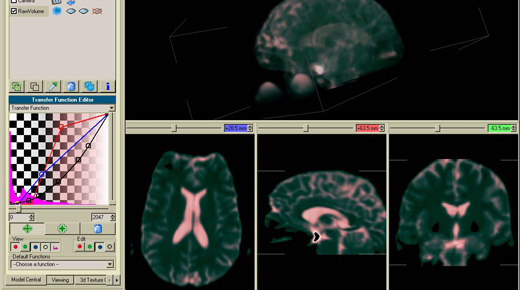
As I’m sure many of you know, the ISO 13485 standard for medical devices was updated in 2016, which means the time to transition your quality management system (QMS) is now. Most auditing organizations have either cut off ISO 13485:2003 recertifications or will be doing so very soon.
ADVERTISEMENT |
I was recently at a client’s location helping the company through its 2016 transition audit when an auditor from one of the largest notified bodies mentioned that less than 3 percent of its U.S. clients are ready to transition to ISO 13485:2016. As a leader in the quality consulting arena, we wanted to share some of our tips and best practices to make sure your organization is ready to ace its transition audit.
We’ll focus on the inclusion of a new requirements for quality system software validation in ISO 13485:2016. Section 4.1.6 outlines the process for validating computer software used in the quality system as follows:
“The organization shall document procedures for the validation of the application of computer software used in the quality management system. Such software applications shall be validated prior to initial use and, as appropriate, after changes to such software or its application.
…
Add new comment