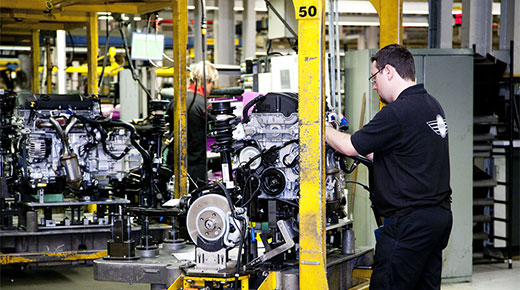
General Motors (GM) recently published updated customer-specific requirements for IATF 16949 compliance. The new requirements take effect Nov. 1, 2017, and cover layered process audit (LPA) requirements in greater depth than previous versions.
ADVERTISEMENT |
LPAs use a series of frequent audits to check high-risk processes and known problem areas. Big changes to GM’s LPA requirements focus on scheduling, organizational participation, and performance improvement. Let’s examine the most important updates, and how automation makes compliance simpler.
Organizationwide engagement in audit
GM’s new customer-specific requirements are clear that LPAs must include top management, adding a new requirement for all departments in the organization to participate.
…
Add new comment