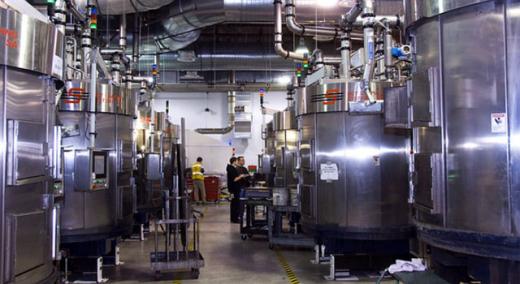
In manufacturing, standardization in production and process control leads to increased profitability and cuts down on many siloed problems that can plague even the most quality-focused organization. But when you have multiple, disparate plants around the country or the globe, standardization can seem unattainable, as each site operates more like an island with its own way of doing things.
ADVERTISEMENT |
I previously worked with one company that had numerous plants throughout the United States and Europe. Over time, each site had developed unique practices. One specific issue that came up was whether to use the metric system for quality data collection. Unfortunately, the company did not standardize. So, when it was time to run cross-plant reports, the results were in different units, presenting a challenge to comparative analysis.
In contrast, I worked with a separate organization that was very adamant about using a standardized approach and implementing the same quality management system at every site. Standardization made it easy to deploy the system to approximately 80 plants in merely 18 months. In addition to streamlining deployment, standardization enabled the company to perform enterprisewide reporting for better decision-making.
…
Comments
Standardization
Hello Eric, just want to say I completely agree with you about standardization. For 10 years I worked as Quality Assurance Manager in a plant making polypropylene based non-woven fabrics. We had a plant in Washington State, another in South Carolina, and a third in Sweden. I tried very hard to move to the type of standardization you talk about, primarily with respect to measurement methods, units, and to a lesser degree names and analytical methods. My motivation often stemmed from sales inquiries with the question, Which plant's product best matched the prospective customer's needs? Because we had no standardization this often involved some type of round-robin testing of current samples in one of the plants and/or our corporate lab. A giant waste of time. The Swedes and I were all for standardization but never could get approval for action. The "cloud" wasn't an option at the time.
Glad to see you are with InfinityQS International. Working for another company we used this tool and over two years went from a five user license to a twenty five user license in manufacturing with floor and lab input for analysis and reporting.
Standardization
Getting the management systems ( ISO 9001, 14001 .. ) documented, cerified and audited throgh same external providers, implementing 5 S at all locations can be useful tOO.
Add new comment