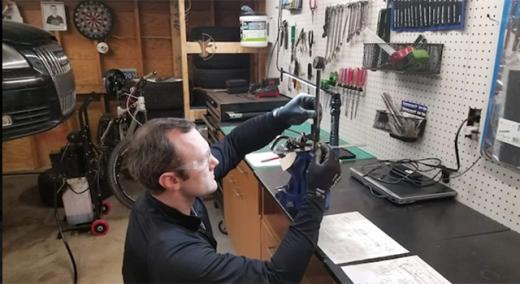
With most industries shifting to remote work due to the Covid-19 pandemic, companies are looking at how they can innovate the work-from-home experience. Toyota’s Ann Harbor, Michigan, research and development team was set to complete the automaker’s newest generation of the Sienna in March 2020. However, after the state went under lockdown, the team was forced to complete the minivan from home.
ADVERTISEMENT |
According to the team, they were still able to see a production trial of the latest Sienna at Toyota’s Indiana plant prior to the lockdown. This gave the team enough ideas on what kind of changes they needed to make to the vehicle. The real challenge was how they were going to do it from home. Toyota Chief Engineer Monte Khaer shared that the later phase involved what they call “fit-and-finish optimization,” which can be difficult to accomplish by just relying on CAD.
Toyota Engineer Kyle Steinkamp works on the new Sienna minivan with his own tools from home. (Image courtesy of Toyota)
…
Add new comment