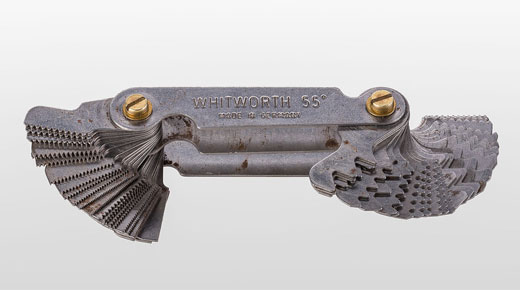
The importance of quality management cannot be overstated. It enables companies to increase efficiency, lower risks, achieve compliance, and build better and safer products. Yet many quality management teams struggle to communicate the value of their operations to other departments and executive leadership.
ADVERTISEMENT |
This inability to communicate the positive outcomes that result from quality initiatives is not only frustrating but also diminishes their value. The fact is, the quality department may be the most transformative within the company. However, without the right numbers to tell its story, it can’t be an effective agent of change and will be seen as another cost center.
So how common of a challenge is this? In a recent blog post, analyst Dan Jacob of LNS Research revealed that 37 percent of LNS survey respondents had answered that quality metrics were not effectively measured at their companies. Jacob notes that the results of that survey had changed little over time.
…
Add new comment