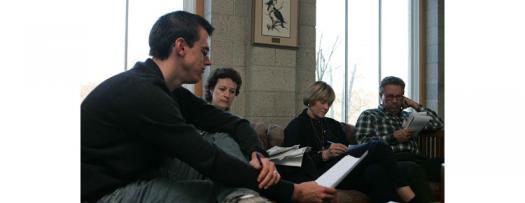
Return on investment (ROI) is the subject of many discussions about ergonomics, and rightfully so. Musculoskeletal disorders are an expensive and preventable workplace injury, with total costs averaging nearly $30,000 per case, according to data from the Occupational Safety and Health Administration (OSHA). Redesigning work areas to match human capabilities not only reduces injury costs, but it also can improve job performance and enhance quality.
ADVERTISEMENT |
The cost of many ergonomics improvements can be justified solely on the productivity and quality benefits associated with the change. This results in the ability to implement a greater number of ergonomics improvements. Ergonomics team members can benefit from defining the ROI of their improvements and communicating it effectively.
However, consider the following limitations when initiating the discussion.
Too much focus on ROI for safety can undermine safety as a core value. It raises the question of whether profits are more important than the safety of people. Are we making the workplace safer only when it is more profitable to be safer?
…
Comments
ROI for Safety
A couple of points Mr. Barker left out of his otherwise important and very valuable discussion: you cannot consider Safety ROI without taking into account risk at the same time. While the CEO is an extremely valuable employee, the risk to the worker on the shop floor is far higher and therefore justifies a higher investment based on ROI.
A second point that we should all think about is that each and every one of us makes these sorts of decisions on a daily basis. Which car do we choose to drive to work, the little gas sipper that will get flattened in a moderately bad accident, or the one ton dually that will smash anything that hits it (except a larger truck.) Which route do we take, a faster more dangerous road or a quiet but meandering back street. Do we continue using our older household tools (or Grandma's kitchen appliances - my sister swears by her 1930 vintage Toastmaster toaster) or do we scrap them in favor of the lastest in safety devices. Each time we are confronted with one of these choices, we are confronted with the price of safety and unconsciously, whatever we decide, we are putting a price on our lives and property.
Importance of Safety ROI
I agree with Mr. Barker that any ROI must be performed in conjunction with having a purpose. I have been doing that for over 30 years. The importance, to me, of Safety ROI is the need to change Safety Actions, both large and small and have those changes becoming daily habits. People do not like change and often times the Company Management wants change becase they have experienced losses from accidents, injuries, etc. Creating a change environment whether for a new process or for a saftey concern requires a plan that needs to address the audience as well as the investment in the change. ROI is an investment calculation, one that the beancounters, stock holders and stake holders want to see. I have had my fair share of CEO's who have literally said how much they value a safe working environment for their employees only to then act quite differently because they want that safe environment at no cost or a cost that would not produce results. Saftey ROI removes the window dressing and treats this as any other business investment and should provide a projected and measured ROI.
Add new comment