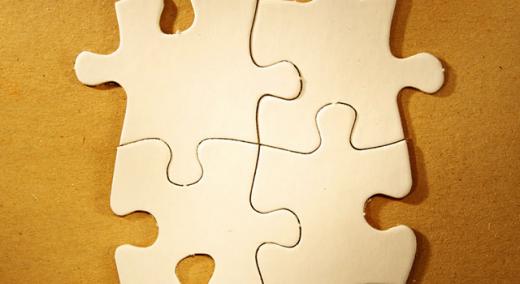
Manufacturers are acutely aware that audits and recalls are just part of business. At the same time, they all agree that the best way to deal with recalls is to prevent them in the first place. Because today’s manufacturers operate on razor-thin margins with little room for error, a reactionary approach to quality management is a massive Achilles’s heel.
ADVERTISEMENT |
In May 2021, Ford Motor Co. had to recall 661,000 Explorer SUVs due to quality issues related to roof covers detaching. This significant recall could cost Ford tens of millions of dollars. Recalls of this nature in manufacturing are far from rare, and events occur across every sector. Whether considered collectively or privately, the market impacts are staggering.
On the surface, it may seem simple: If quality is built into production, quality products will emerge from production. However, products and processes are becoming more complex, and efforts to reduce cost and increase transparency only compound the challenges to sustaining high quality levels.
…
Add new comment