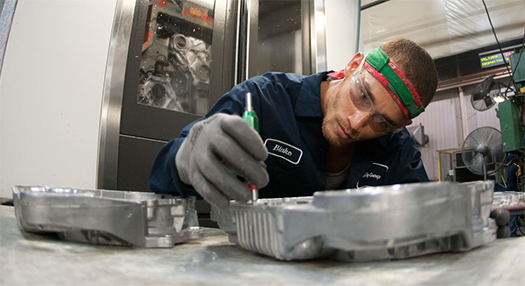
Body
This is the fourth part in a series about my perspective of what the future has in store for various aspects of manufacturing. I approached each aspect by imagining what is possible using what we know to be technically possible today. In part one I covered cutting tools for machining, in part two production management, and in part three inventory management.
ADVERTISEMENT |
…
Want to continue?
Log in or create a FREE account.
By logging in you agree to receive communication from Quality Digest.
Privacy Policy.
Add new comment