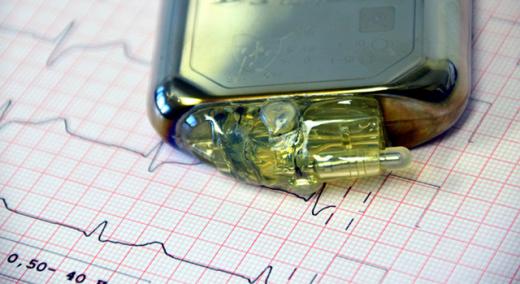
Believe it or not, paper is very expensive. Although the going rate for a ream of standard copy paper is only about 10 bucks, the expense of relying on paper for your medical device quality management system is downright outrageous.
ADVERTISEMENT |
Some medical device manufacturers have recognized how expensive paper really can be and therefore rely on spreadsheets and documents—so-called “digital paper,”—only to realize this variation of paper is just as expensive, if not more so, due to the false sense of security digital file systems can give.
If you’re still relying on these outdated systems, let’s consider three key ways paper ends up costing significantly more than $10 per ream.
Loss of company valuation
We had an eye-opening conversation with Ronny Bracken, executive and principal at Paladin Biomedical Consultants, an accomplished medical device research and development executive with a career spanning more than two decades. In addition to his role helping his clients in all manner of regulatory and engineering services, Bracken invests in early-stage medical device companies.
…
Add new comment