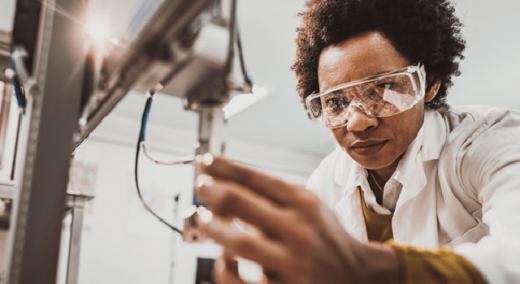
During the Sept. 18, 2020, session of the “National Conversation with Manufacturers,” our three West Coast manufacturing leaders on the panel kept coming back to their critical need for skilled workers.
ADVERTISEMENT |
The conversation was one in a series of 11 virtual listening sessions hosted by the National Institute of Standards and Technology’s Hollings Manufacturing Extension Partnership (NIST MEP). The purpose of the listening sessions was learning how small and medium-sized manufacturers across the country have been handling the near-term jolt from the Covid-19 pandemic and preparing for success in the long-term.
…
Add new comment