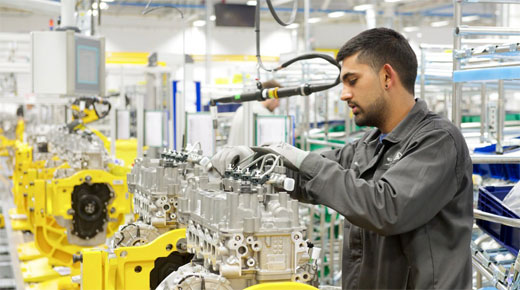
Want to improve something? You’ve got to measure it first. If you’re motivated to improve product quality and reduce manufacturing costs, the first step in establishing a successful statistical process control (SPC) solution is getting some data. And if you want to make good decisions from those data, you better make sure you measure the right things.
ADVERTISEMENT |
But you also must trust in the accuracy of the information—and you’ll need to prepare a convenient means of analyzing it. Otherwise, why go to the time and expense of collecting it?
With some forethought on your part, SPC data collection can set the stage for significant process and product improvements. Your SPC system can become the foundation for greatly reducing risk, waste, and defects. But if you want it to work right, you’ll need to take a hard look at the very first step.
How do you collect data?
…
Comments
What to measure and using the outcome
The choice of what to measure is critical: We need to challenge if the learnings from the measure will lead to a basis for action... Will a point outside the process limits (not spec limits) catalyse action? If not, worth pursuing?
I think we need a system in place where routinely collected data are used to discover what's going on, and the (working) system provides time allowance to perform investigations and also have the time to profit from the learnings by implementing the actions plans coming from the learnings. Here we need a means of focusing on the "big signals" that should give more return for the time and effort and energy invested.
Agree that the consolidation of the sheer volume of data we can collect these days becomes more and more important. Not easy but the consolidation needs to be simple and effective. Traditional approaches struggle here. When a good consolidation is achieved, higher-level priorities can be defined, again providing a basis for (value-added) action.
All the above can bring continual improvement: Who'd argue against that?
Add new comment