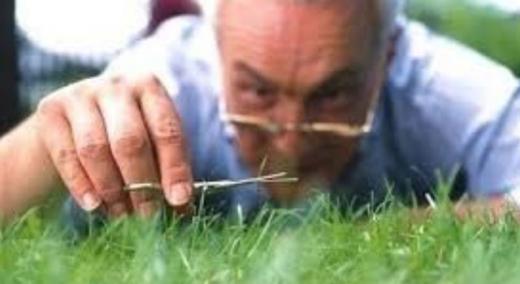
Obsessive-compulsive disorder (OCD) is an anxiety condition characterized by intrusive thoughts that produce uneasiness, apprehension, fear, or worry (collectively termed obsessions), along with repetitive behaviors (or compulsions) aimed at reducing the associated anxiety.
ADVERTISEMENT |
For team members in quality departments, I personally feel that many OCD traits ought to be a unique selling point for recruitment. In fact, the level of attention to detail inherent in many with OCD is the penchant driving quality systems and processes in most organizations. It’s the compulsive checking-rechecking cycle that teaches the importance of verification and validation.
How can you tell if people with OCD work in your quality department? Symptoms of the disorder include: excessive washing or cleaning, repeated checking, hoarding, relationship-related obsessions, aversion to particular numbers, and nervous rituals such as opening and closing a door a certain number of times before entering or leaving a room.
…
Comments
OCD
" It’s commonly understood that if employees in the quality department are hated, they’re doing their job quite effectively." << seriously ?? You must work in a completely different environment like we had in the 70s & 80s. If we used that mentality, there would be a line to talk to the HR dept.
The problem is OCD checking & re0-checking won't be satisfied. Whether something checks good or bad they will continually re-check in case their initial 20 checks were made incorrectly.
Add new comment