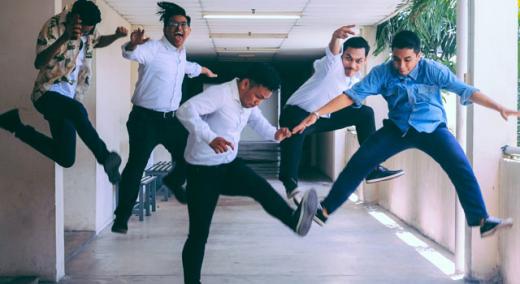
Without the perfect balance of efficient workers, adequate resources, and satisfied customers, manufacturing businesses risk sending their operations into a tailspin.
ADVERTISEMENT |
Workforce optimization (WFO) streamlines manufacturing workflow by cutting costs and increasing productivity—allowing you to equilibrate critical manufacturing tasks such as product planning, resource allocation, staff scheduling, and product shipping.
Here, we’ll show you four tips that will help you easily optimize your workforce.
1. Implement better communication systems
It’s time to think outside of the suggestion box—a good bottom-up communication system allows the plant management and the factory floor to better coordinate. This prevents work-related misunderstandings that can lead to poor product quality, delays in the production process, and workers feeling like they aren’t appreciated.
In any manufacturing plant, the factory floor workers have the information on why production is slacking, what machines are acting up, and why there are a lot of late deliveries—and they might have ideas to solve these issues.
…
Add new comment