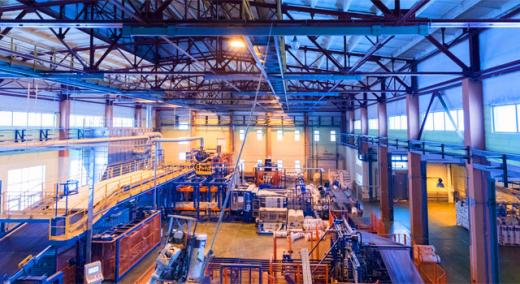
In a customer-centered world, meeting customers’ needs is more demanding and business-critical than ever. Simultaneously, manufacturers struggle to reduce operating costs as margins compress and the competitive landscape intensifies. This dichotomy and a pressure to “choose” between reducing costs and delighting customers is not mutually exclusive.
ADVERTISEMENT |
Best-in-class manufacturers recognize there’s no trade-off; they take a holistic approach to quality management that allows them to excel in both arenas. A quality-driven mindset across every layer of an enterprise strategically enhances process visibility and compliance to enable improvements in both cost and customer satisfaction.
The trade-off mindset
![]() |
For many discrete manufacturers, delivering more robust customizations at a reduced margin or choosing to settle for less than zero-defect quality in favor of cutting operating costs is part of the old trade-off mindset.
…
Add new comment