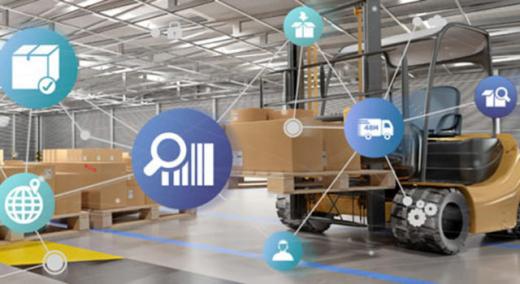
Most manufacturers want a quality management system (QMS) to meet strict quality values. They need one to expressly meet the needs of their specific organization yet be within the parameters of federal, state, and industry prerequisites.
ADVERTISEMENT |
For example, food, drug, and medical device companies all face many of the same regulatory standards, needing wide-ranging quality controls. But in some cases, countries and even states have different types of reporting schemes. The regulatory agencies not only need the data, but they also want it in the format that they dictate. How it gets reported in Maine can be different than in Spain.
So, to meet standards in their various regulatory constituencies, such products must ensure quality control, standardized testing, quality assurance, and compliance with common industry and well-established regulatory standards. There needs to rigorous testing to make sure the product is safe for humans to ingest and distributed at the correct strength to meet desired outcomes.
…
Add new comment