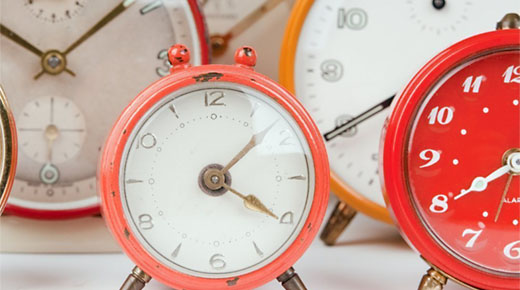
I always enjoy my fellow columnist Arun Hariharan’s musings. He has worked in the field of quality for more than 30 years and, like me, has obtained reasonable results. But he has also made his share of the inevitable growing-pain mistakes—lessons we both had to learn the hard way in an environment totally different from today’s.
ADVERTISEMENT |
I would like to share some of his thoughts about qualities that make one successful as an improvement professional regardless of circumstances. This column will focus on one of the most important.
Ability to execute or implement
“Farming looks mighty easy when your plow is a pencil and you’re a thousand miles from the corn field.”
—U.S. president Dwight Eisenhower (1956)
Hariharan: “I’ve come across a few armchair philosophers who became quality professionals. They would complain that nobody in the business listened to them. I’ve learned that one of the most important qualities needed to be successful in quality is the ability to execute. Few people in the business will be interested in theories alone; the quality person must work with their colleagues in the business to implement what they preach.”
…
Comments
We need to stop parroting Deming, Juran and Shewhart
Davis, I've known you a long time. You just told us that it took 30 years for Deming's 4-day seminar to kick in.
Like most Lean Six Sigma training, that's too long.
Last century quality was about manufacturing. 21st Century quality is about Agile application of seven key tools in services (e.g., healthcare).
Let's stop talking about the history of quality and start talking about the future of quality.
I absolutely agree with you, Jay!
Let's just say that my 30 years of Deming (and Juran) study has made me "agile" in my ability to teach and practice their brilliant concepts without the usual "historical pontification."
Note that my self-assessment includes increasing the number of plots one produces of data plotted over time. Simple, intelligent assesment of these will then lead to the more efficient use of the other tools you recommend.
I have evolved to consulting with fewer, simpler tools and have never been so effective. I guess the study got me fluent in a "language" that paves the way for a "future" based in "built-in" 'improvement' (as opposed to most current efforts mired in "bolt-on" 'quality'). Many people are still stuck in parroting vis-a-vis this needed fluency.
Add new comment