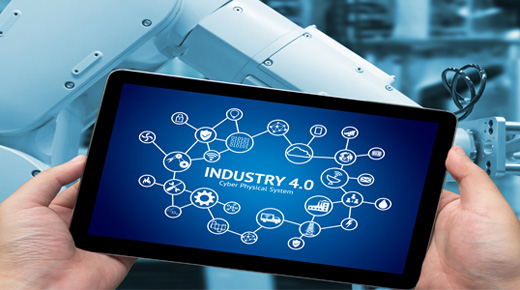
Industry 4.0, also known as smart factory 4.0, is labeled as the fourth industrial revolution, yet many don’t understand it or how it will affect the things they do; quality management is no exception. The executives in your organization, however, are most certainly monitoring this paradigm-shifting strategy. Quality professionals should be as well to ensure they are part of their company’s Industry 4.0 dialogue.
ADVERTISEMENT |
As quality professionals forge into this new era, it’s critical to have a solid understanding of the premise and aspects of Industry 4.0 and its implications for production, the extended supply chain, and their quality management systems (QMS).
…
Add new comment