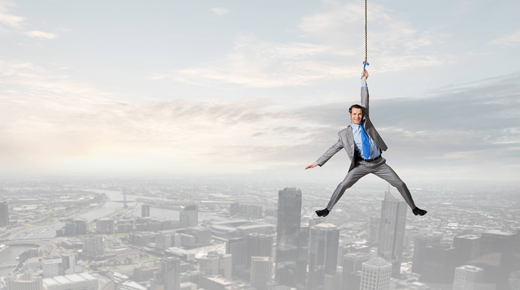
ISO 9001:2015 has significant structural changes that differentiate it from the previous standard. The new high-level structure is common to all ISO management system standards (i.e., quality, environmental, IT security) and enables us to start looking at integration of these systems. There is a standard core text and structure and, important for ISO 9001, there is now the inclusion of services.
ADVERTISEMENT |
Risk-based thinking is widely recognized as driving the new standard but it is not immediately obvious that this thinking flows right through the quality management system (QMS). The term “documented information” replaces “documents and records.” This points to a vital understanding that information must flow through the QMS and not be just a collection of static records.
System thinking is needed and this is not complicated. We are used to process thinking which means following a series of steps in a regular order. System thinking means looking at the linkage between processes and how information flows between processes. A record is an information output from a process and becomes the information input to the next process.
…
Comments
Risk Based Thinking
Good read.. gives insight on the importance of risk-based thinking in ISO..
Add new comment