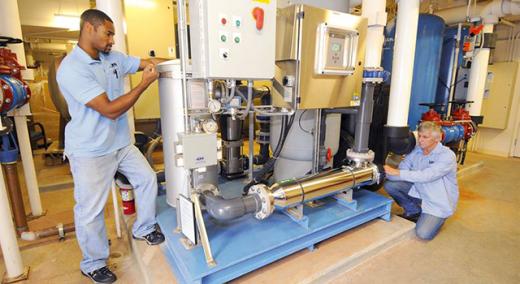
Whether we’re talking to a front-line operator, a plant manager, or CEO, people’s reactions to being assigned a new recurring task are remarkably similar: “Oh great—more to do.” Sound familiar?
ADVERTISEMENT |
It’s a reaction that’s common in organizations transitioning from paper-based to an automated digital process for layered process audits (LPAs), even though the end result may be a sharp reduction in defects and simpler audit processes. Although there are numerous benefits to moving from a paper-based to a mobile digital platform for your LPA program, the focus of this article is how to make the transition as smooth as possible.
Layered process audits focus on quick, straightforward elements of process inputs, helping ensure process standardization and reduce defects upstream from the point of manufacture. Automating LPAs can involve a transition process, one made easier by adopting a pilot program to help you learn as you go. Here we discuss different types of pilot programs, as well as some best practices to ensure success.
…
Add new comment