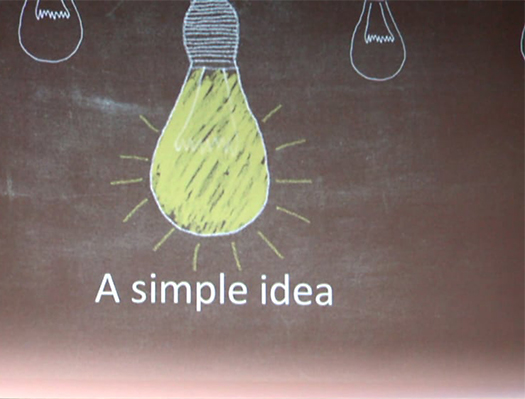
Compliance is a common term that is very broad, and many companies interpret compliance as a host of different items. It can be related to quality, safety, or operations, but it encompasses a long list of areas within the organization, including financial, risk, governance, sustainability, and more. Companies try to fit this broad category of compliance into a single term, which can be a daunting feat. However, compliance is not the only component on which companies should be focusing
ADVERTISEMENT |
As a definition, compliance is the adherence to a set of guidelines, usually ones that organizations are not necessarily in control of. It’s created by a standards body, a regulatory agency, government regulations, or a requirement to do business in certain industries. Compliance, in a sense, is doing “what’s required.”
…
Comments
Quality & Compliance
Quite a useful read.. throws light on why both quality and compliance are impoirtant...
Add new comment