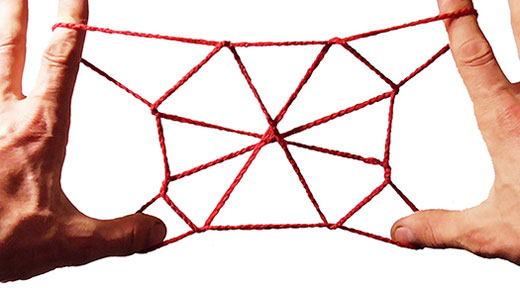
Sponsored Content
Particles of metal in children’s medicine. Adulterated baby formula. Spontaneously combusting smartphones. When scandal is only a tweet away, companies can’t hide from quality failures.
ADVERTISEMENT |
High-profile quality problems like these can not only harm consumers, but also lead to huge remediation costs, damaged brand perception, and risk of legal and regulatory actions to the parent company and its suppliers. More than ever, it’s critical for today’s companies to maintain the highest level of quality.
Reducing costs while trying to enhance margins have driven many organizations to use a range of global suppliers and external manufacturing partners. Operational norms have evolved, but many organizations have been slow to invest in modern quality systems and technology infrastructure. As a result, these companies continue to manage quality and compliance activities with disconnected legacy systems, further complicated by a series of appended manual steps and workarounds.
…
Add new comment