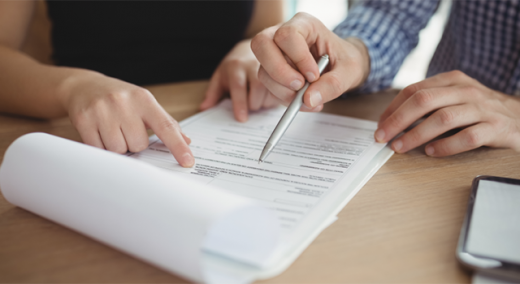
For medical device manufacturers, finding success means setting ourselves up for success with repeatable processes that not only ensure quality but also mitigate future risk.
ADVERTISEMENT |
This drive for quality is the reason we have such hyper-specific language in our standards. It’s what demands the stringent expectations from our regulatory bodies before products hit the market. It’s also why any examination of internal processes in our quality management systems focuses on the idea of continuous improvement.
Correcting mistakes means more than meets the eye. We’re not only undoing a wrong when it comes to an internal error; we also are preventing this or other similar mistakes from occurring again. This spirit is paramount to achieving quality, reliability, and success in an industry that demands all three as a bare minimum for entry.
The same can be said for our relationships with suppliers. Whether they’re manufacturing our devices, creating specialty parts, or just helping deliver the raw materials used in our manufacturing processes, a mistake on their side has the same effect as one on ours.
…
Add new comment