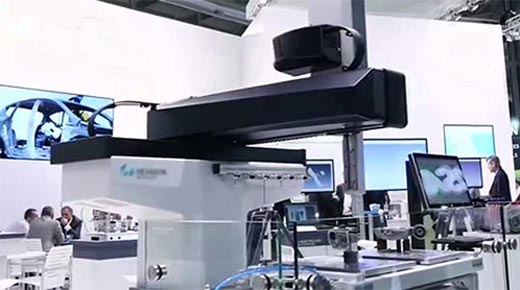
Closed-loop manufacturing and the digital thread are new buzzwords being thrown around a lot these days, but do we understand their significance? In all manufacturing processes, there are three key elements consisting of “sensing, thinking, and acting” that drive your manufacturing productivity. Most of us in the quality field think of sensing as only a measurement system and the results as their sole contribution; however, there is much more to consider about the function of this key element in the overall production workflow.
ADVERTISEMENT |
…
Add new comment