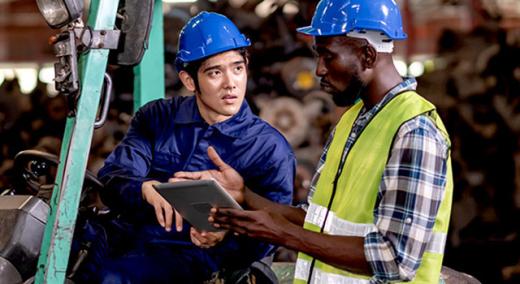
Gemba walks are an essential tool to understand the challenges of your manufacturing frontline. Each manufacturing facility is unique. The best way to solve your unique operational challenges is to perform a gemba walk focused on specific goals.
ADVERTISEMENT |
This article will outline the fundamentals of a gemba walk and teach you how to tailor your gemba ealk to solve frontline challenges.
What is a gemba walk?
Initially developed by Taiichi Ohno, founder of the Toyota Production System, the basic concept of a gemba walk is to get first-hand experience of the processes that you are trying to improve. Ohno believed that management should actively visit and observe operations to identify waste and find opportunities for improvement.
…
Add new comment