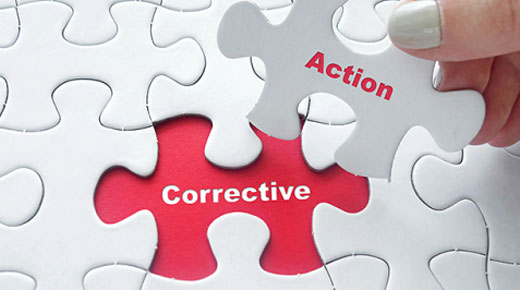
We raise the corrective and preventive action (CAPA) topic often because it is still something that companies tend to struggle with and find themselves in hot water over, particularly when it comes to regulatory audits or inspections.
There’s often a sense that CAPA is another inconvenient process that takes resources away from those preferred revenue-generating tasks, but in reality, failing to give CAPA appropriate focus can cost a company greatly. Could your company be making any of the common mistakes that tend to happen?
ADVERTISEMENT |
We’re looking at five issues here:
1. CAPA metrics
This can be summarized as the way we measure the effectiveness and productivity of our CAPA activities. A big mistake (and one which I’ve been guilty of myself) is in how metrics are established, and which ones are given focus to assess the “health” of CAPA in the company. A common one is “time to close a CAPA.”
…
Comments
timeliness of capa
dear sir, finally u tried to say is no timeline for capa ?pls provide the answer pls sir
Add new comment