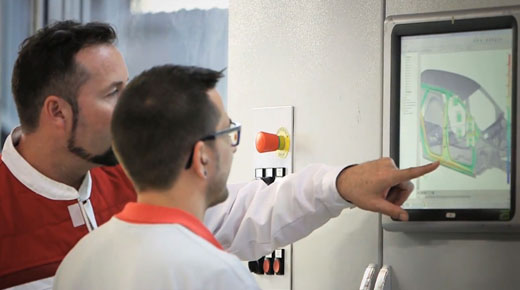
The execution of an inspection plan is critical for ensuring the continuous production of quality products. The purpose of this article is to explain how software tools can be used to maximize utilization of the inspection system within the main control loop once the inspection plan has been created.
ADVERTISEMENT |
In my previous article, "Get the Scoop on Closed-Loop Manufacturing," the essential elements of a closed-loop manufacturing process were discussed. One of those essential elements, referred to as the sensing element, is where the inspection system acquires measurement data needed for the control element in a repetitive manufacturing environment. Continuous measurement is needed for an efficient manufacturing process and therefore preferable to doing inspection planning outside of the main control loop. In this way, the inspection plan can be deployed on the inspection system with minimal interruption to the main control loop.
…
Add new comment