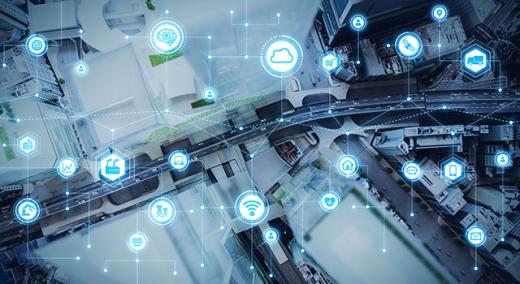
As commercialization strategies evolve amid Covid-19, and supply chains continue to trend toward diversification, the only way for businesses to control their destiny is to double down on quality standards. If cash is king, then quality is the king’s closest confidant since high quality protects and guides the bottom line.
ADVERTISEMENT |
To gain a competitive edge, many businesses are planning to digitize their supply chains so they can use real-time data to infuse quality safeguards into all the materials and products they buy, move, and sell through their entire supply chain. In a July 2020 survey of more than 200 companies conducted by QIMA, two-thirds of respondents reported that the pandemic has accelerated their company’s path toward digitizing their supply chain, including the use of new digital inspection and audit solutions.
Here are some of the ways digital transformation can help businesses enhance quality throughout their supply chain networks.
…
Add new comment