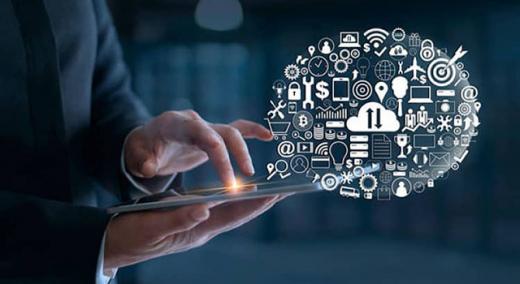
Although previous industrial revolutions were driven by steam machines and the dawn of electricity, the unfolding fourth industrial revolution is being powered by digital technologies, such as cloud computing, machine learning, and the internet of things. Accompanying the fourth industrial revolution is Quality 4.0, a recently coined term referring to the rapid changes in value-chain performance excellence we’re seeing amid digital transformation.
ADVERTISEMENT |
Notably, it’s the greater availability of data that’s pushing Quality 4.0 forward. As the global economy becomes increasingly digital, metrics are all the more critical for establishing quality standards and ensuring smooth operations. Companies that effectively manage data points across the supply chain—ranging from their suppliers to customers—will gain a significant advantage in driving Quality 4.0, and thus performance excellence.
…
Add new comment