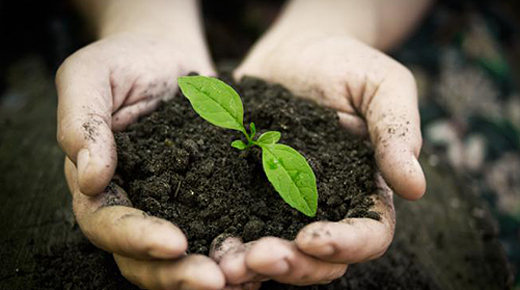
Certifications often drive the implementation of a system approach, based on ISO standards. The primary implementation demand is for ISO 9001. Certifications do have initial costs and then recurring costs for surveillance and recertification visits. This is a responsive approach to business requirements, invariably driven by a forthcoming contract that mandates the system approach. Prudent businesses appreciate the risk of not having a process-based system.
ADVERTISEMENT |
When budgets are tight, supply chains are challenging, and retaining employees is difficult, it is all the more essential that organizations invest in a good management system. As W. Edwards Deming said, “A bad system will let down a good person every time.”
…
Comments
Certification
While self certification may be an option, it is not a wise option. Systems will deteriorate and, even with the rigor of regular external audits, it is the rare organization that does not find issues while preparing for those audits.
Add new comment