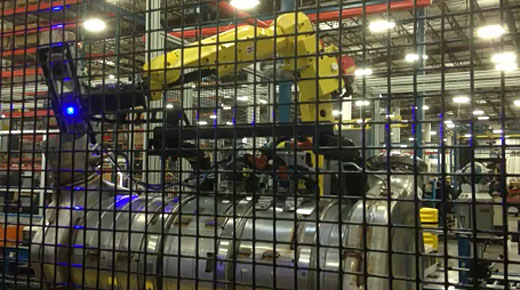
Sponsored Content
Headquartered in Algona, Washington, Dynacraft is a diversified global manufacturer of PACCAR medium and heavy-duty truck parts sold under the Kenworth, Peterbilt, and DAF nameplates. For more than 40 years, Dynacraft has provided the company’s truck manufacturing divisions and PACCAR parts division with high-quality components, subassemblies, and specialized services.
ADVERTISEMENT |
The challenge
“One of the requirements going into the new 2017 emission systems, which we are producing currently, was a requirement from our supplier quality group to do a 100-percent inspection of the emissions assemblies,” explains Mario Caudillo, production quality engineer at Dynacraft. “We were performing a standard sampling plan up to that point, so it was quite a challenge to try to go from a sample plan to 100-percent inspection.”
…
Add new comment