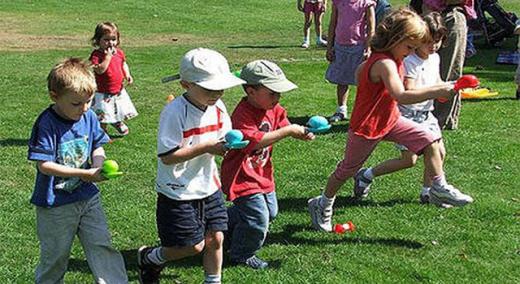
If you’re looking for information on medical-device design controls and product development, you can find a practically endless number of articles, videos, and podcasts with a few quick online searches. Yet with so much out there on these topics, there’s a glaring omission of a closely related subject: design transfer.
ADVERTISEMENT |
Not only is design transfer left out of many guides and overviews of the product life cycle, it’s also relegated to just a single sentence in 21 CFR Part 820: “Each manufacturer shall establish and maintain procedures to ensure that the device design is correctly translated into production specifications.”
If that sounds too vague to be of much help, you’re not alone. With so much uncertainty around design transfer, let’s take a closer look at the process, when it should happen, and what it should entail.
What happens during design transfer?
The basic definition of design transfer is the process by which a medical device’s design is transferred to production. However, this is a deceptively simple way of explaining a much more complex and ongoing process.
…
Add new comment