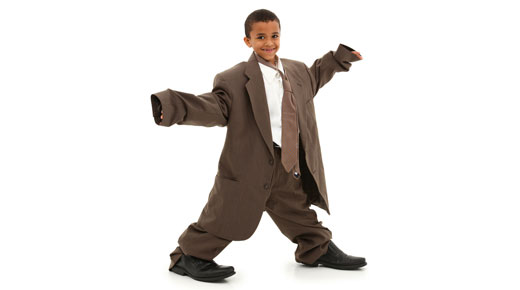
Your CMS can't be too small or too big
Body
Medical device startups tend to share many common issues. They are usually striving for better resources (such as people and capital) as well as the knowledge and expertise required to deal with the U.S. Food and Drug Administration (FDA) and successfully bring a product to market.
ADVERTISEMENT |
For many startups, a quality management system (QMS) might not appear to be a priority, but I’m here to tell you it needs to be.
…
Want to continue?
Log in or create a FREE account.
By logging in you agree to receive communication from Quality Digest.
Privacy Policy.
Add new comment