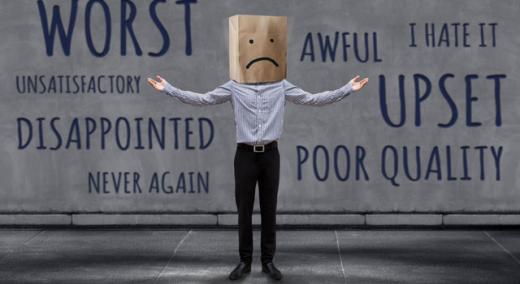
When is a product “good enough” to accept? This is the classic challenge of quality. High customer expectations demand that suspect products be thoroughly scrutinized and a high standard set for their release. Customers expect this, and quality staff strive to achieve it.
ADVERTISEMENT |
The other side of the tug of war is cost. Business leaders are looking for every advantage they can get in reducing their costs, and scrap products are one of the biggest targets out there. Sometimes it seems that quality leaders and business leaders don’t even speak the same language. Quality leaders talk with great animation about “doing the right thing for the customer,” while business leaders talk in terms of time and money.
Does it have to be this way? Can quality and business be on the same side?
In short, the answer is yes. What is required is a change in language, attitude, and approach about quality. The two models below help to illustrate the different attitudes about quality. The tool is a cost-of-quality metric set. There are generally two schools of thought on quality cost behavior. The opposing viewpoints are illustrated below.
…
Add new comment