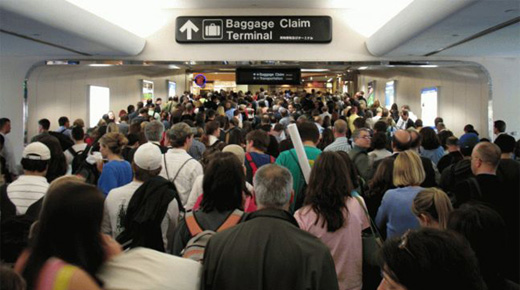
A recent article in The Wall Street Journal (“The Reason Southwest Stopped Overbooking”), which contained excerpts from an interview with Southwest Airlines’ CEO Gary Kelly, brought out the need to address airline capacity issues on the ground and in the air. Responding to a question on the impact of lack of infrastructure improvements, Kelly made the following comment.
ADVERTISEMENT |
“In the air, it makes their trips longer and longer. A flight today from New York to Dallas is significantly longer for scheduled flight times than it was 20 years ago, and that’s true for city pairs across the U.S. When we experience these longer flight times, we change the schedule so that they’re no longer “delayed” according to the schedule, but now all you’ve done is you’ve built in the delay time into the schedule, and I just fear that as time goes by over the next generation that there’s a limit to how much you can simply increase the flight times before you just reach gridlock.”
…
Add new comment