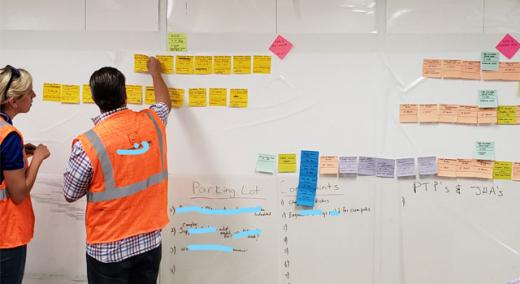
When we look at a Personal Kanban, its simplicity belies its power. Visualizing our work as individuals, as teams, and even as teams of teams creates trust, reliability, and understanding. When we want to coordinate work, these are serious prerequisites.
ADVERTISEMENT |
The image below is from a construction trailer, they are engaged in a lean construction exercise known as a “pull-plan.” Each color is a different contractor; each diamond is a delivery or a milestone. In this case we have five different contractors whose daily work relies on the completion of daily work done by the other contractors.
A construction team planning work openly and honestly
To spell this out, their work directly relies on people in other companies, every day.
…
Add new comment