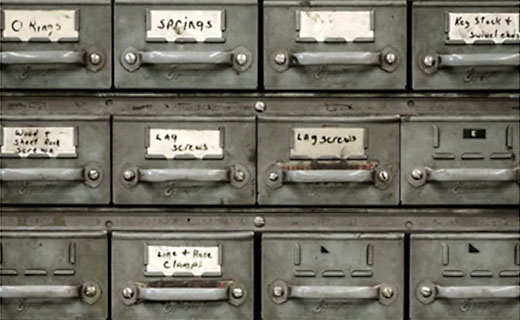
When James Womack and Daniel Jones published Lean Thinking in 1996, they offered the world a book that collected the core principles of a key operational model. Though not stated directly, they created a profile for the Toyota Production System (TPS) that was revelatory and highly useful, adding a deeper logic to JIT, standard work, kanban, load leveling, and other associated operational mechanisms.
The impact of that book (and its model) was nothing short of dazzling. Its elements work—and work well together. Finally, a way of contemplating the war on waste (muda) that is drawn broadly enough for it to apply not just to many work venues but to any work venue. This was a coup and a contribution of a very high order. Plus, the lean thinking model positions marketing and sales as a partner to operations, a surprise to many at the time.
…
Add new comment